The application of ultra-fine grinding machine in the pharmaceutical industry
The medical ultra-fine grinder used in the development of medical resources can produce micron-level powder, which can destroy the structure of the tissue cell wall and obtain the required material characteristics.
The medical ultra-micro grinder uses compressed air to be cooled, filtered, and dried. The nozzle forms a supersonic airflow and is injected into the crushing cavity. The material is fluidized under the action of pressure difference. The accelerated material is at the intersection of multiple nozzles. Converge, produce fierce impact, collision, friction, and shear to achieve ultra-fine grinding of particles, which can be used to produce various micron-level powders. The medical ultra-fine grinder is used for ultra-fine pulverization and wall-breaking processing of various types of medicine; improvement of drug solubility; ingenious confusion and evacuation of compound drugs; manufacture of film ointment, etc.
The scope of use is:
Chinese herbal medicine: Typical materials include American ginseng, ginseng, Ganoderma lucidum, pearls and other valuable materials and pollen, hawthorn, shiitake mushrooms, pearl powder, gallnut, multiflorum multiflorum, Andrographis paniculata, mint, houttuynia cordata, fern root, kudzu root, dry alum, yam, white peony root , Lotus leaf, white tuckahoe, Tianqi, Angelica dahurica, honeysuckle, cordyceps, saffron, cuttlefish, fumarole, Radix isatidis, etc.
Western medicine: Typical materials include stomach medicine, nimodipine, antibiotic medicine, contrast medicine, etc.
- The medical ultra-fine grinderis small in size, light in weight and easy to operate.
- The medical ultra-fine grinderhas low vibration and impact and low noise.
- The medical ultra-fine grinderhas high frequency, large amplitude and high efficiency. The discharging granularity is fine and the distribution is even.
- The medical ultra-fine grinderis equipped with unique feeding and discharging ports, which is convenient for dust-free collection.
- Intermittent sealed grinding of pharmaceutical ultra-fine grinder may also be continuous open-circuit grinding.
- The medical ultra-fine grinderis easy to clean. The grinding drum can be removed and opened to facilitate cleaning and disinfection without leaving dirt.
- The grinding cylinder of the medical ultra-fine grinderis made of stainless steel. The ultra-fine grinderuses air separation, heavy pressure grinding, and shearing to achieve ultra-fine grinding of dry materials. It is composed of cylindrical crushing chamber, grinding wheel, grinding rail, fan, material collection system and so on. The jet mill uses high-speed airflow to superfinely grind materials to ensure no wear and pollution.
Selection of medical crusher equipment:
According to the physical characteristics of medicine, two kinds of equipment are used for grinding processing. For sugar-free and oil-free products, the grading impact mill (effectively reducing the energy consumption of production equipment) can achieve the grinding effect; for sugar-containing and oily products, use a fluidized-bed jet mill (low crushing temperature) , Oiliness and sugar will not melt during ultra-fine grinding, resulting in adhesion of equipment) for grinding processing.
Measures to avoid blockage of superfine grinder
The ultra-fine grinder is a fully closed circuit pulverization that reduces the extrusion pressure, increases the roller speed, and combines with the classifier. Jet mills use high-speed airflow to superfine materials. They mainly include horizontal disc jet mills, 0-type circulating tube jet mills, counter-jet jet mills, target jet mills, and fluidized bed air jets mill. The jet mill uses the forms of collision, friction, and shear to achieve ultra-fine pulverization of dry materials. The ultra-fine grinder consists of a cylindrical pulverizing chamber, grinding wheel, grinding rail, fan, material collection system, etc..
After the compressed air is filtered and dried, it is sprayed into the crushing chamber at high speed through the Laval nozzle. At the intersection of multiple high-pressure airflows, the materials are repeatedly collided, rubbed, and sheared to be crushed. The crushed materials rise with the suction of the fan. The airflow moves to the classification zone. Under the action of the strong centrifugal force generated by the high-speed rotating classification turbine, the coarse and fine materials are separated. The fine particles that meet the particle size requirements are collected by the cyclone separator and dust collector through the classification wheel, and the coarse particles descend to the crushing zone and continue to be crushed. The jet mill has the advantages of high efficiency, low noise, reliable working performance and product quality, safe operation, and low material loss. The jet mill has simple structure, firmness, stable operation and good crushing effect. The inner wall of the casing is processed smoothly, which avoids the phenomenon of rough inner wall and powder accumulation, so that the production of medicine, food and chemical industry can meet the requirements of GMP.
Clogging of the ultra-fine grinder is one of the common faults, mainly caused by improper operation, increased load, and too fast feeding speed. Operate the superfine grinder correctly to prevent clogging.
(1) During the feeding process, always pay attention to the deflection angle of the ammeter pointer. If it exceeds the rated current, it indicates that the motor is overloaded, and the motor will be burnt if overloaded for a long time. Therefore, the current when the pulverizer is working is generally controlled at about 85% of the rated current.
(2) When the feeding speed is too fast, the feeding port should be reduced or closed immediately. You can also control the amount of feeding by adding a feeder to change the feeding method.
(3) Due to the high speed, large load, and large load fluctuation of the ultra-fine grinder, improper matching with the conveying equipment will cause the discharge pipe to weaken or be blocked and there will be no wind, which will cause the tuyere of the ultra-fine grinder to be blocked. Adjust the output volume in time to make the equipment operate normally.
(4) Excessive water content of crushed materials will cause the superfine crusher to block.
(5) Broken and severely aged hammers should be replaced regularly to keep the grinder in good working condition and check the screen regularly, which can not only improve the production efficiency, but also prevent the ultra-micro grinder from clogging and improve the reliability of the grinder.
Ultra-fine grinder helps the development of lithium battery materials
The ultra-fine grinder has a uniquely designed grading chamber and a grading wheel with frequency conversion speed regulation. It does not need to be equipped with a screen and can classify the product size at a low speed. The circulating feed structure not only strictly limits the "large particles", but also avoids excessive crushing, so the product has a narrow particle size distribution. The classification wheel is used for classification, which avoids the difficulty of passing the powder with more than 150 mesh.
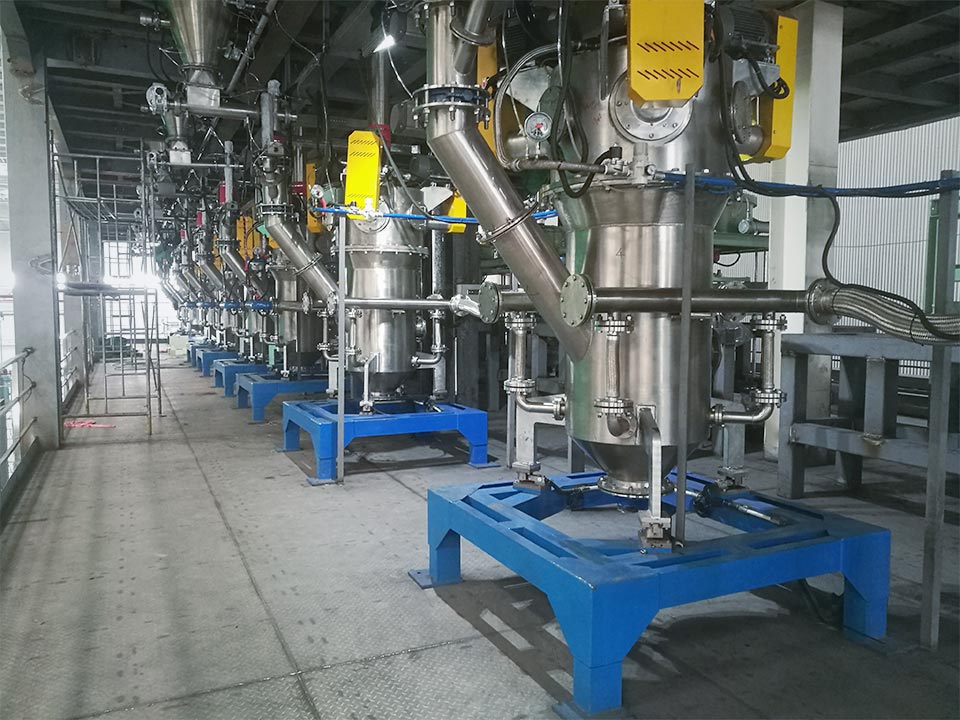
The main wear parts of the ultra-fine grinder: flat teeth, round teeth, large and small grinding teeth. The flat teeth and round teeth are made of stainless steel and have a good dynamic balance. If they are severely worn, they should be replaced. The size of the self-made metal processing should be specified, and the weight difference of each piece shall not exceed 1g to avoid vibration damage to the bearing and the machine.
At present, ultra-fine grinders have been used in batches for the cathode materials of lithium batteries, mainly including lithium cobalt oxide, lithium nickel oxide, lithium manganate, lithium nickel cobalt manganate (ternary material) and lithium iron phosphate. The crushing of the cathode material is a very critical process. Currently, commonly used equipment includes jet mills, mechanical mills, and sand mills.
As the capacity of the lithium-ion battery increases, the internal energy stored increases, and the internal temperature will increase. In severe cases, a short circuit may occur, thereby damaging the battery. Coating high-purity ultra-fine alumina on the surface of PP, PE or multilayer composite diaphragm can improve the safety of lithium-ion batteries.
What is the working principle of the ultra-fine grinder? The high-speed airflow generated by the air source system enters the pulverizing system, causing the material to rotate at a high speed, and the material collides with the material to achieve the purpose of ultra-fine pulverization. When materials enter the grading system, only materials that meet the particle size requirements will be collected, and those that do not meet the particle size requirements will be sent back to the crushing chamber to continue crushing. Repeat this process until the material meets the standard. The ultra-fine grinder can be used for the pulverization of chemical raw materials and non-metallic minerals.
Ultrafine grinding of dry and hard solid materials
In the modern industry, there are many follow-up products that require ultra-fine grinding of materials, such as black tea, ultra-fine grinding of tea leaves, such as ultra-fine grinding of rice husk powder, used to make special bags; ultra-fine grinding of silicon carbide, Used in various industries, etc., etc., are inseparable from the ultra-fine grinder.
The modern ultrafine grinder can set different types of pulverization for different materials, and can also customize different sizes of ultrafine grinder according to the size of the output. This modern ultrafine grinder has large output, low noise, convenient cleaning, sturdiness and durability. It is in line with the current trend of ultrafine grinding of materials and has become the new darling of current fashion.
The ultra-fine grinder is especially suitable for ultra-fine grnding of dry materials and hard materials. The grinding process is finer and the output is larger. The hard carbon powder structure of diamond can be ultra-finely pulverized, and the requirements of modern ultra-fine grinder for materials are as dry as possible.
The ultra-fine grinder is completely carried out in a closed environment when performing ultra-fine grinding, will not produce dust spills, and protect the working environment of workers. It is a very environmentally friendly mechanical equipment. According to the different grinding media, the ultrafine grinder is divided into jet pulverizer and mechanical grinder. The jet mill can be filled with air or special gas for ultra-fine grinding to ensure the integrity of the material. The mechanical crusher can be divided into many types, small rod crushing, etc. The specific principle is to perform ultrafine crushing through the collision of materials and equipment. However, no matter what kind of ultrafine grinder, it is very environmentally friendly in the process of grinding materials. The output can range from one catty to more than 100 catties per hour, and the fineness varies from a few hundred meshes to thousands of meshes.
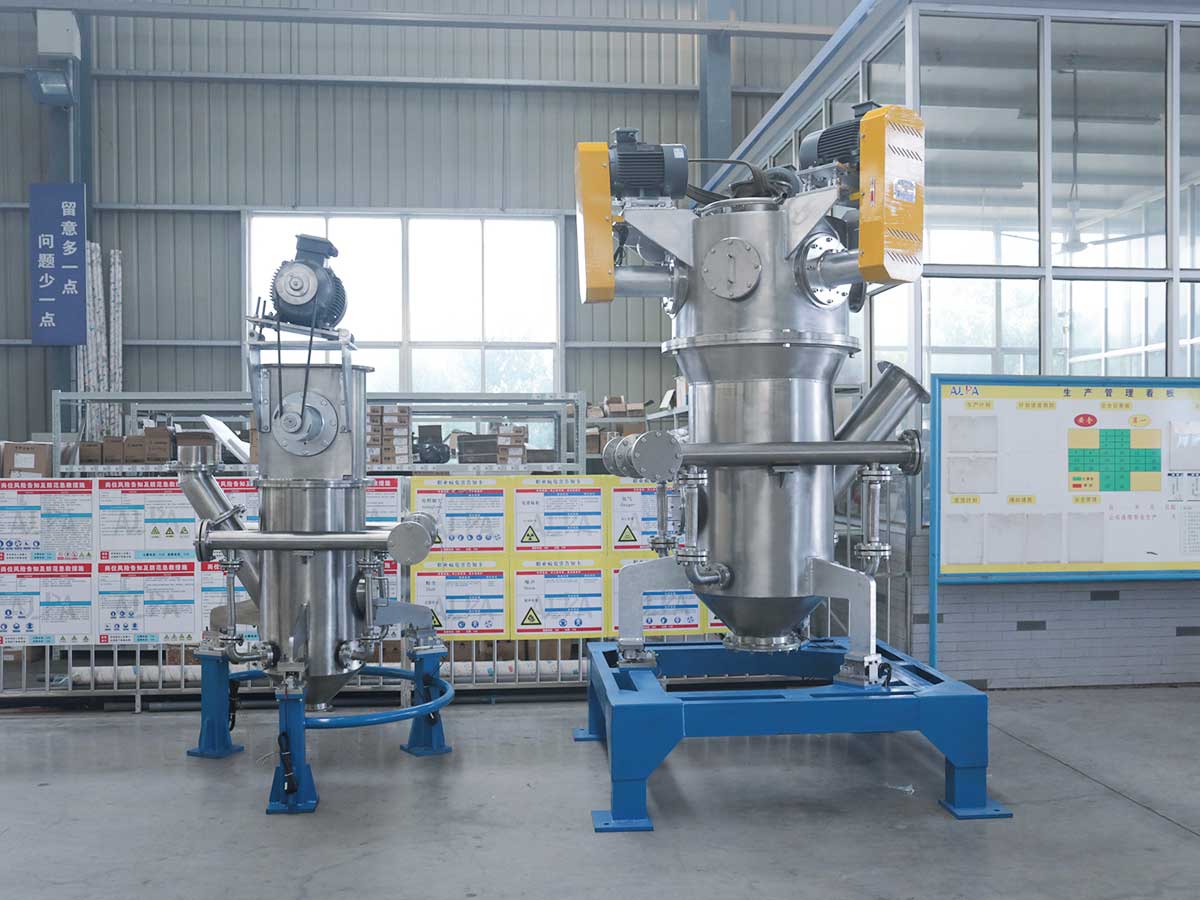
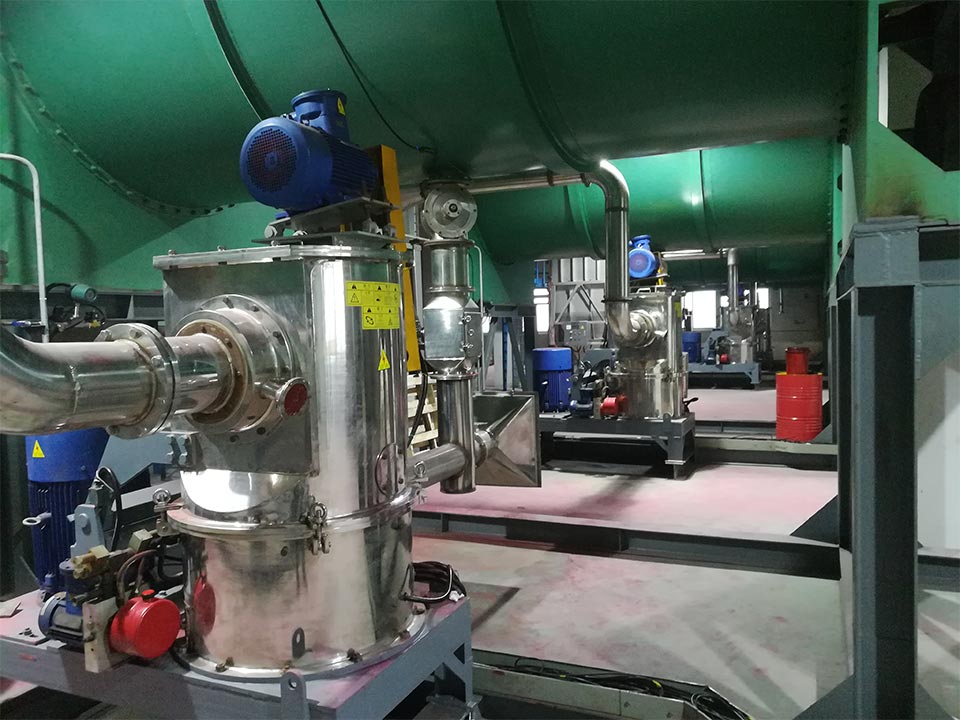
With the development of the times, ultra-fine grinders are used in chemical, mining, abrasives, refractory materials, battery materials, metallurgy, building materials, pharmaceuticals, ceramics, food, feed, new materials and other industries and the ultra-fine grinding of various dry powder materials. Dispersion and other aspects have been widely used. It is suitable for dry grinding of various materials with Mohs hardness below 9 and is especially suitable for the grinding of materials with high hardness, high purity and high added value. The crushed material has good particle shape and narrow particle size distribution.