Powder Spheroidization
With the development of powder application, its performance requirements are getting higher and higher. In addition to low impurity content, finer particle size, strict particle size distribution, it also needs to have a certain particle morphology. The morphology of the particles has an important influence on many properties of the particle group, such as the specific surface area, fluidity, filling property, chemical activity, and adhesion of the powder.
Spherical powder, especially highly dispersed spherical powder, has good fluidity due to its spherical structure, larger specific surface area and its own physical and chemical properties, making it more play a role in the field of application.
Powder Spheroidization Introduction
(taking carbon anode graphite as example)
Carbon material is currently the main negative electrode material used in lithium-ion batteries, and its performance affects the quality, cost and safety of lithium-ion batteries.
In addition to raw materials and process formulas, which determine the performance of negative electrode materials, it is also one of the important factors to provide equipment and technologies such as carbon graphite milling, spheroidizing, shaping, and classifying with stable performance and high efficiency and energy saving.
Milling stage
Whether it is artificial graphite or natural graphite, it is milled multiple times through several sets of CSM710 units (the naming method of each manufacturer is different) to become D50:20μm powder. According to the different raw materials, the number of milling is also different: for example, big natural graphite is generally milled 4 to 6 times, artificial graphite is generally milled 1 to 3 times.
Spheroidization stage
Generally, they tend to use a system of CSM410 and horizontal high-precision turbo classifiers for shaping. The classifier is used to remove fine powder produced by shaping in time. According to the different raw materials, the number of shaping is different. Natural graphite generally 8-12 times of shaping, artificial graphite generally 2 to 4 times of shaping.
Natural flake graphite spheroidization process
Raw materials are milled by a single set of CSM710 special milling machine, particle size of raw materials is milled to a fine powder with particle size of D50: 21-23μm, which is convenient for the next process to be spherical. Through the CSM510 type spheroidizing machine equipped with the FW260 high efficiency classifier series unit process, the particles are prepared into spheroidized graphite particles with particle size of D50: 19-20μm, and CSM410 spheroidizing machine is equipped with FW230 high efficiency classifier series unit. Change the particle size to D50: 15-17μm potato-shaped graphite particles;
Artificial graphite spheroidization process
Raw materials are uniformly sent to the CSM710 special mill single set series unit through the screw feed for ultra-fine grinding. Raw material particle size is milled to D50:23-25μm fine powder, which is convenient for the next process to be spheroidized. Through 3 sets of CSM510 type spheroidizing machines equipped with FW260 high-efficiency classifiers and several sets of series unit processes, the particles are prepared into graphite powder with particle size of D50: 19-21μm, and the required qualified potato-shaped balls are obtained through the special graphite surface modification and shaping equipment.
Comparison of milled particle size of graphite spheroidization technology
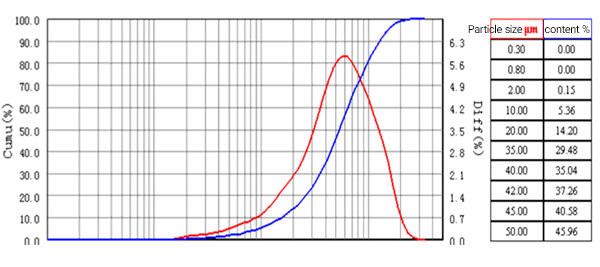
Graphite carbon raw material
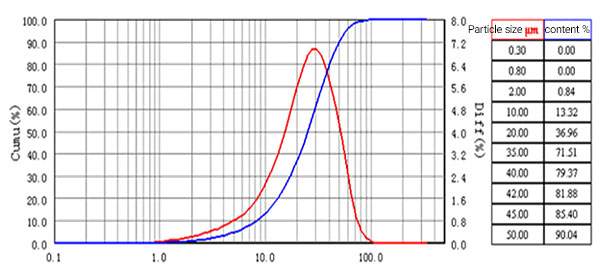
Milled by CSM710
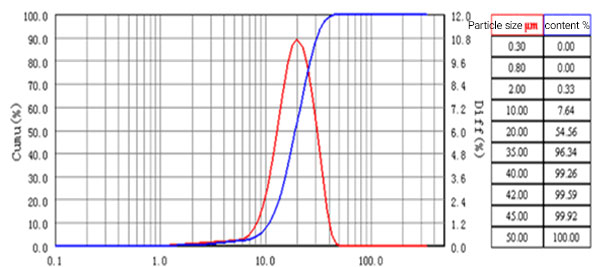
Spherical by CSM510
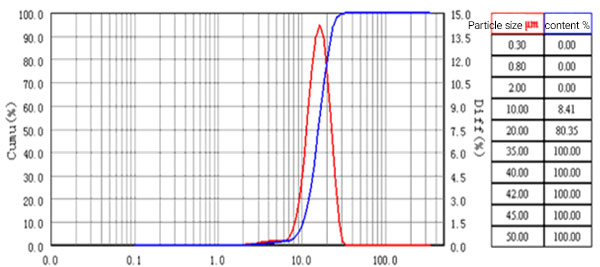
Shaping by CSM410
Application of several spherical powders
Because the spherical powder has better performance, it is widely used in new technology and new products.
Application of spherical silica powder
At present, spherical silicon powder is widely used in large-scale integrated circuit packaging and is gradually used in high-tech fields such as aviation, aerospace, fine chemicals and special ceramics. It is an important filler in epoxy resin system, which can reduce at least 30% epoxy resin consumption has a good market prospect.
Spherical silica powder advantages:
1) The surface fluidity of the powder is good, the filling amount of powder can be increased in the integrated circuit packaging. In this way, the smaller the coefficient of thermal expansion, the better the dielectric capacity, the longer service life of produced electronic devices, the better performance;
2) The plastic seal formed after spheroidization has low stress concentration, high yield, shortens the production cycle, and reduces the possibility of product damage during transportation;
3) The surface morphology of the particles after spheroidization is regular, which reduces the wear of the mold during the production and processing of the finished product, reduces the cost, and prolongs the service life of the mold.
Application of high-performance spherical Titanium powder
As an advanced lightweight and high-strength metal material, titanium is widely used in aerospace, automotive industry, chemical, biomedical and other fields. High-performance spherical titanium powder has the characteristics of high sphericity, good fluidity, high loose density, low oxygen content (<0.15%) and fine particle size. It is mainly used in advanced powder metallurgy technology, laser additive manufacturing technology, and thermal spraying technology. And other fields.
Application of spherical Metal powder
Spherical metal powder is the core raw material for metal 3D printing. With the rapid development of metal 3D printing technology, the market for spherical metal powder will maintain a high growth trend. In 2016, the market size of 3D printing metal powder was approximately US$250 million.
Application of spherical Alumina
1) Spherical powder has good compression molding and sintering ;characteristics, which is conducive to the production of high-quality ceramic products;
2) As grinding and polishing material, spherical alumina can avoid scratches;
3) In the petrochemical industry, spherical alumina powder can be adjusted by adjusting the particle size configuration to control the pore size and distribution of the catalyst carrier particles;
4) The spherical alumina used directly as a catalyst can reduce abrasion and increase the service life of catalyst, thereby reducing production costs.