Application of Ultra-fine Grinding Technology in Food Processing
Ultra-fine grinding technology is a new technology developed in the past 20 years. The so-called ultra-fine grinding refers to the use of mechanical or hydrodynamic methods to overcome the internal cohesive force of solids to grind them, thereby grinding the material particles of more than 3 mm to 10-25 microns. A material processing high-tech produced by the development of high-tech. Ultra-fine powder is the final product of ultra-fine grinding. It has special physical and chemical properties that ordinary particles do not have, such as good solubility, dispersibility, adsorption, and chemical reaction activity. Therefore, ultra-fine powders have been widely used in many fields such as food, chemicals, medicine, cosmetics, pesticides, dyes, coatings, electronics and aerospace.
- Technical Features
Fast speed and low temperature grinding: The ultra-fine grinding technology uses supersonic jet grinding, cold slurry grinding and other methods, which is completely different from the previous pure mechanical grinding methods. There will be no local overheating during the grinding process, and it can even be ground at a low temperature. The speed is fast and can be completed in an instant, so the biologically active ingredients of the powder are retained to the greatest extent, so as to facilitate the production of the required high-quality products .
Fine particle size and uniform distribution: Due to the use of supersonic airflow grinding, the distribution of forces acting on the raw materials is quite uniform. The setting of the classification system not only strictly restricts large particles, but also avoids over-grinding, and obtains ultra-fine powder with uniform particle size distribution. At the same time, the specific surface area of the powder is greatly increased, so that the adsorption and solubility are correspondingly increased. .
Save raw materials and improve utilization: After the object is ultra-finely ground, the ultra-fine powder with a near nanometer particle size can generally be directly used in the production of preparations, while the products of conventional grinding still need some intermediate links to meet the requirements of direct use and production , This is likely to cause waste of raw materials. Therefore, this technology is especially suitable for grinding precious and rare raw materials.
Reduce pollution: Ultra-fine grinding is carried out in a closed system, which not only avoids the pollution of the surrounding environment by micro-powder, but also prevents dust in the air from polluting the product. Therefore, by using this technology in food and medical health products, the microbial content and dust can be effectively controlled.
- Grinding method
Grinding medium grinding: Grinding medium grinding is the process of grinding material particles by means of the impact generated by the moving grinding medium (grinding medium) and the non-impact bending, squeezing and shearing forces. The grinding media pulverization process is mainly grinding and friction, namely extrusion and shearing. Its effect depends on the size, shape, ratio, movement mode, filling rate of the material, and the mechanical characteristics of the grinding of the material. There are three types of typical media grinding equipment: ball mill, stirring mill and vibration mill.
The ball mill is a traditional equipment used for ultra-fine grinding, and the product size can reach 20-40 microns. When the particle size of the product is required to be below 20 microns, the efficiency is low, the energy consumption is large, and the processing time is long. Stirring mill is developed on the basis of ball mill, mainly composed of grinding container, agitator, disperser, separator and feed pump. When working, under the action of centrifugal force generated by the high-speed rotation of the disperser, the grinding medium and the particle slurry produce impact shearing, friction and squeezing to grind the particles. The stirring mill can achieve ultra-micronization and homogenization of product particles, and the average particle size of the finished product can reach a few microns at least. Vibration mill is to grind particles by using the effects of impact shear, friction and extrusion produced by high-frequency vibration of the grinding medium. The average particle size of the finished product can reach 2-3 microns or less, and the pulverization efficiency is much higher than that of the ball mill. The processing capacity is more than 10 times that of a ball mill with the same capacity.
Airflow ultra-fine grinding: The jet mill can be used for ultrafine grinding. It uses compressed air or superheated steam, and the supersonic high turbulent airflow generated by the nozzle as the carrier of the particles, and the impact backlog occurs between the particles or between the particles and the fixed plate , Friction and shearing, etc., so as to achieve the purpose of grinding. There are six major types of airflow stainless steel grinders: disc type, circulating tube type, target type, collision type, rotary impact type, and fluidized bed type. Compared with ordinary mechanical ultra-fine stainless steel pulverizer, the airflow stainless steel pulverizer can grind the product very fine (the fineness of the powder can reach 2-40 microns), and the particle size distribution range is narrower, that is, the particle size is more uniform. Because the gas expands at the nozzle to reduce the temperature, there is no accompanying heat during the grinding process, so the grinding temperature rise is very low. This feature is particularly important for ultra-fine grinding of low-melting and heat-sensitive materials. However, the energy consumption of air jet grinding is large, and the energy utilization rate is only about 2%, which is several times higher than other grinding methods.
It is worth pointing out that it is generally believed that the particle size of the product is directly proportional to the feeding speed, that is, the larger the feeding speed, the larger the product particle size. This understanding is not comprehensive. This statement is reasonable when the feeding speed or the particle concentration in the stainless steel pulverizer reaches a certain value. Because the feeding speed increases, the particle concentration in the stainless steel pulverizer also increases, and particle crowding occurs. Even the particles flow like a plunger. Only the particles at the front of the "plunger" have the possibility of effective collision. The particles only collide and rub each other at a low speed, and generate heat. However, this does not mean that the smaller the particle concentration, the smaller the product size, or the higher the grinding efficiency. On the contrary, when the particle concentration is low to a certain level, there will be no chance of collision between the particles and the grinding efficiency will be reduced.
Ultra-fine grinding of non-metallic minerals
Non-metallic mines, metal mines, and fuel mines are called the three pillars of the materials industry. The use of non-metallic minerals depends on the degree of deep processing, including ultra-fine grinding, ultra-fine grade, fine purification and surface modification, among which effective ultra-fine grinding is the prerequisite and guarantee for various deep processing. The ideal ultra-fine powder should have the characteristics: particles as small as possible, no agglomeration, narrow particle size distribution, spherical particles as much as possible, uniform chemical composition, etc.
Due to the wide variety of non-metallic minerals, various requirements are put forward on the particle size distribution and purity of crushed products according to their different uses. The development of ultra-fine grinding technology must adapt to its specific requirements. Generally speaking, the requirements for non-metallic minerals are as follows:
- Fineness
The application of non-metallic mineral products requires a certain degree. For example, kaolin and heavy calcium carbonate as papermaking raw materials require a product fineness of -2μm accounting for 90%, whiteness >90%; high-grade paint filler heavy calcium carbonate powder fineness of 1250 Mesh; zirconium silicate as a ceramic opacifier requires an average fineness of 0.5~1μm; wollastonite as a filler also requires its fineness to be less than 10μm and so on.
- Purity
The purity requirement of non-metallic mineral products is also one of its main indicators, which means that no pollution should be allowed during the grinding process, and the original composition should be maintained. If it is white minerals, a certain degree of whiteness is required. For example, the whiteness of calcined kaolin and talc used in papermaking is required to be ≥90%, and the whiteness of heavy calcium carbonate used in papermaking coatings, fillers and high-grade paint fillers is greater than 90%. Wait.
- Powder shape
Some non-metallic mineral products have strict requirements on their shapes to meet different needs. For example, wollastonite used for composite reinforcement, its ultrafine powder is required to maintain its original needle-like crystal state as much as possible, so that wollastonite products become natural short fiber reinforced materials, and its aspect ratio is required to be >8~10.
The application fields of ultra-fine powder materials account for 40.3% in the mechanical field, 34.6% in the thermal field, 12.9% in the electromagnetic field, 8.9% in the biomedical field, 2.4% in the optical field, and 0.9% in other fields.
Non-metallic mineral ultra-fine grinding method
Crushing is different from the destruction of a single material. It refers to the effect on the group, that is, the crushed material is a group of particles with different sizes and shapes.
There are two main methods for preparing ultrafine powder from the principle of preparation: one is chemical synthesis; the other is physical grinding. Chemical synthesis is through chemical reaction or phase transformation, the powder is prepared from ions, atoms, and molecules through crystal nucleus formation and crystal growth. Due to the complex production process, high cost, and low yield, the application is limited. The principle of physical grinding is to grind materials through the action of mechanical force. Compared with chemical synthesis methods, physical grinding has lower cost, relatively simple process, and large output.
Advantages of mechanical grinding method: large output, low cost, simple process, etc., and mechanochemical effects are generated during the grinding process to increase the activity of the powder; disadvantages: the purity, fineness and morphology of the product are not as good as the ultra-fine powder prepared by chemical method body. This method is suitable for large-scale industrial production, such as deep processing of mineral products.
Non-metallic mineral ultra-fine grinding equipment
At present, the main method for preparing ultra-fine powder materials is physical grinding. Therefore, ultra-fine grinding equipment mainly refers to various grinding-related equipment that mainly produces ultra-fine powder by mechanical methods. Commonly used ultrafine grinding equipment includes jet mill, mechanical impact mill, vibration mill, stirring mill, colloid mill and ball mill.
Equipment type | Feeding size/mm | Product fineness d97/μm | Grinding principle |
Jet mill | <2 | 3~45 | Impact, collision |
Mechanical impact grinding | <10 | 8~45 | Blow, impact, shear |
Rotary mill | <30 | 10~45 | Impact, collision, shear, friction |
Vibration mill | <5 | 2~74 | Friction, collision, shear |
Stirring mill | <1 | 2~45 | Friction, collision, shear |
Drum Ball Mill | <5 | 5~74 | Friction, impact |
Planetary ball mill | <5 | 5~74 | Friction, impact |
Grinding and peeling machine | <0.2 | 2~20 | Friction, collision, shear |
Sand mill | <0.2 | 1~20 | Friction, collision, shear |
Roller mill | <30 | 10~45 | Squeeze, friction |
High pressure homogenizer | <0.03 | 1~10 | Cavitation, turbulence, shear |
Colloid mill | <0.2 | 2~20 | Friction, shear |
- High-speed mechanical impact mill
High-speed mechanical impact crusher refers to the use of rotating bodies (rods, hammers, blades, etc.) rotating at a high speed around a horizontal or vertical axis to apply a violent impact on the feedstock, causing it to collide with the fixed body or particles, thereby making An ultra-fine grinding equipment for particle grinding.
Advantages: large crushing ratio, adjustable fine powder particle size, simple structure, easy operation, less supporting equipment, compact installation, less floor space, large capacity, and high efficiency.
Disadvantages: high-speed operation makes overheating and component wear unavoidable.
It is suitable for the production of superfine powder of medium hardness materials such as calcite, marble, chalk and talc.
- Jet mill
Jet mill is also called jet mill or energy flow mill. It uses the energy of high-speed airflow (300-500m/s) or superheated steam (300-400℃) to cause particles to collide, collide and rub each other, thereby causing solid materials to grind. Mainly include: flat jet mill, circulating jet mill, opposite jet jet mill, rake jet mill, fluidized bed jet mill, etc.
The jet mill pulverization ratio is generally 1-40, and the product fineness d can generally reach 3-10μm. The product is less contaminated and can be operated in a sterile state. It is suitable for pulverizing low-melting and heat-sensitive materials and biologically active products. The production process is continuous, the production capacity is large, and the degree of self-control and automation is high.
Disadvantages: Jet mill is currently the most researched ultrafine grinding equipment with the most complete models and relatively mature technology. It also has the following shortcomings: large-scale, specialized production of high purity, high fineness products, high cost, high energy consumption, The machining accuracy is difficult to reach sub-micron products, and the material is worn out. Jet mills are widely used for ultrafine grinding of non-metallic minerals, chemical raw materials, health foods, rare earths, etc., such as talc, marble, kaolin, and other non-metallic minerals below medium hardness.
Vibration mill is an ultra-fine grinding equipment with a ball or rod as the medium. The processed product can be as fine as a few microns. It is widely used in building materials, metallurgy, chemical industry, ceramics, glass, refractory materials and non-metallic minerals and other industries. Powder processing.
Advantages of vibration mill: compact structure, small size, small quality, simple operation, convenient maintenance, low energy consumption, high output, uniform product size, disadvantages: large noise, large-size vibration mill has high technical requirements for springs, bearings and other machine parts .
The development trend of ultra-fine grinding equipment
(1) Improve product fineness and reduce equipment grinding limit;
(2) Increase the output of a single machine and reduce the energy consumption per unit of product;
(3) Reduce abrasion;
(4) High stability and reliability;
(5) Online control of product fineness and particle size distribution;
(6) Efficient, fine and large grading equipment;
(7) Ultra-fine grinding equipment for special grain and tough materials.
Article source: China Powder Network
Classification and working principle of jet mill
Jet mill, as one of the ultrafine grinding equipment, is also one of the important equipment in the grinding industry. After the compressed air of the fluidized bed pulverizer is frozen, filtered and dried, it forms a supersonic airflow through the nozzles and is injected into the pulverizing chamber to fluidize the material. The accelerated material merges at the intersection of the jet airflows of several nozzles, resulting in violent The collision, friction and shearing of the particles can achieve ultra-fine grinding of the particles.
The ground material is transported to the impeller classification area by the rising airflow. Under the action of the centrifugal force of the classification wheel and the suction force of the fan, the coarse and fine powder are separated. The airflow enters the cyclone separator, the fine dust is collected by the bag filter, and the purified gas is discharged by the induced draft fan. The flat jet mill has a wide range of applications due to its simple structure and easy manufacturing.
Structure: It is mainly composed of crushing chamber, nozzle opening, discharge opening, air flow outlet, compressed air inlet, classification zone, etc.
Working principle: The compressed air or superheated steam is transformed into high-speed air flow through the nozzle. When the material is sent into the crushing chamber through the feeder, it is sheared by the high-speed air flow. The strong impact and intense friction make the material grind into ultra-fine products. It is widely used in ultrafine grinding of non-metallic minerals and chemical raw materials. The particle limit of the product depends on the solids content in the confluent gas stream. Under the opposite ratio of unit energy consumption, the products produced by jet mill are more refined, particle size distribution is more uniform, activity is also greater, and the dispersion performance is better than the price. Due to the Joule-Thomson cooling effect caused by the adiabatic expansion of the compressed gas during the grinding process, some low-melting or heat-sensitive materials can be used in the grinding process.
The classification of jet mills currently has the following five types in the industry. They can be divided into horizontal disc (flat) jet mills, circulating tube jet mills, target jet mills, counter jet jet mills and fluidized bed jet mills.
The principle of airflow grinding: dry oil-free compressed airflow or too many nozzles, high-speed jet drives the material to move at a high speed, causing the material to collide, rub and compress. The crushed material reaches the classification area with the airflow, and the material that meets the fineness requirements is finally collected by the collector . If the material does not meet the required particle size, return to the crushing chamber, continue grinding until the required fineness is reached, and stop setting. Due to the high velocity gradient near the nozzle, most of the grinding occurs near the nozzle. In the crushing chamber, the collision frequency of particles and particles is much higher than the collision frequency of particles and the device wall. In other words, the main grinding effect of jet mill is the collision or friction between particles.
Application, processing technology and development trend of silicon powder
Silicon micropowder is made of natural quartz (SiO2) or fused quartz (amorphous SiO2 after high temperature melting and cooling of natural quartz) after crushing, ball milling (or vibration, jet milling), flotation, pickling purification, high-purity water treatment, etc. The micro powder processed by this technology.
Silicon micropowder is a non-metallic material that is odorless, non-toxic and non-polluting. It has the advantages of high hardness, low thermal conductivity, high temperature resistance, insulation and stable chemical properties.
According to the level of silicon powder, it can be divided into: ordinary silicon powder, electrical grade silicon powder, fused silicon powder, ultrafine silicon powder, spherical silicon powder. According to the purpose, it can be divided into: fine silicon powder for paint and coating, fine silicon powder for epoxy floor, fine silicon powder for rubber, fine silicon powder for sealant, fine silicon powder for electronic and electrical grade plastics, and fine silicon powder for precision ceramics. According to the production process, it can be divided into: crystalline powder, cristobalite powder, fused powder, and various active powders.
Application of silicon powder
According to its different quality grades, microsilica powder can be used in the production fields of rubber, plastics, advanced paints, coatings, refractory materials, electrical insulation, electronic packaging, high-grade ceramics, precision casting, etc.
Ordinary silicon powder is mainly used for epoxy resin casting paint, potting material, welding rod protective layer, metal casting, ceramics, silicone rubber, ordinary paint, coating and other chemical industry fillers. Electrical grade silicon powder is mainly used for insulation casting of ordinary electrical appliances and components, insulation casting of high-voltage electrical appliances, APG (automatic epoxy resin pressure gel molding technology) process injection material, epoxy potting and high-end ceramic glaze industries.
Electrical and electronic grade silicon powder particle size distribution requirements
Specification/Mesh | Median particle size D50/μm | Specific surface area/(cm2/g) | Cumulative granularity |
300 | 21.00~25.00 | 1700~2100 | ≤50μm≥75% |
400 | 16.00~20.00 | 2100~2400 | ≤39μm≥75% |
600 | 11.00~15.00 | 2400~3000 | ≤25μm≥75% |
1000 | 8.00~10.00 | 3000~4000 | ≤10μm≥65% |
Electronic grade silicon micropowder is mainly used for integrated circuits and electronic components plastic packaging materials and packaging materials, epoxy resin casting materials, potting materials and high-grade paints, coatings, engineering plastics fillers, adhesives, silicone rubber, precision casting , High-grade ceramic glaze fillers and other chemical fields. The annual consumption of epoxy molding compound is tens of thousands of tons, and the content of silica powder in the filler accounts for 70% to 90%.
The SiO2 content of high-purity ultra-fine silicon powder is higher than 99.9%, and it has the characteristics of small particle size, large specific surface area, high chemical purity, and good filling ability. Mainly used for large-scale and ultra-large-scale integrated circuit plastic molding compound, electronic component molding compound, epoxy castable potting compound, high-grade coatings, paints, engineering plastics, adhesives, silicone rubber, precision casting, advanced ceramics and chemicals field.
Spherical silicon powder has a high filling rate, and the smaller the expansion coefficient, the lower the thermal conductivity; the plastic packaging compound has the least stress concentration and the highest strength; the friction coefficient is small, and the wear on the mold is small. Mainly used in electronic plastic packaging materials, coatings, epoxy floors, silicone rubber and other fields.
In order to better fuse non-metallic mineral fillers with high molecular polymers, non-metallic minerals must be crushed, purified and modified. Generally speaking, the smaller the particle size of the filler and the more uniform the dispersion, the better the mechanical properties of the product.
Superfine grinding of silicon powder
The use of natural quartz minerals as raw materials to prepare ultrafine powder is not only to meet market demand, but also to better reduce the content of harmful impurities in the powder. Natural quartz mineral contains a large number of inclusions and cracks. The use of ultra-fine crushing technology can greatly reduce the number of cracks and defects. Combined with the purification process, the content of harmful impurities can be better reduced. The preparation of crystalline powder, cristobalite powder, fusion powder and various active powders requires a grinding and classification process.
The choice of ultra-fine grinding and ultra-fine equipment will directly affect the output, quality and shape of the powder particles of the final product. At present, the unit combinations of ultra-fine grinding and ultra-fine grinding equipment include: ball mill plus grading, eccentric vibration mill plus grading, and vibration mill plus grading.
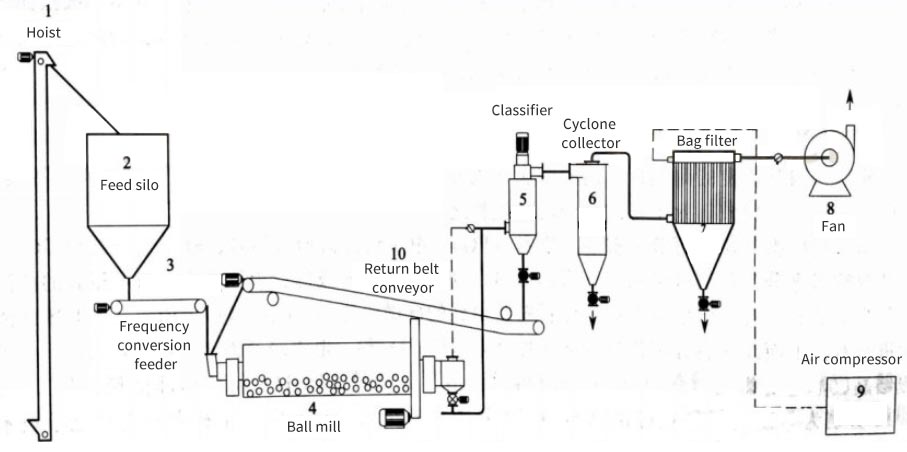
The characteristics of the ball mill classification production line: large output, simple equipment operation, low maintenance costs, flexible selection of grinding media and liners, low pollution to the high-purity processing of materials, reliable overall operation of the equipment, and stable product quality. The application of silicon powder can make the product high in whiteness, good gloss and stable quality index. The production of high-purity ultra-fine silicon powder is obtained by further ultra-fine pulverization or grinding and classification on the basis of the preparation of high-purity sand.
Surface modification of silicon powder
The effect of silane coupling agent applied to the surface modification of silicon powder is very ideal. It can transform the hydrophilicity of silica powder into an organic-philic surface, and can also improve the wettability of organic polymer materials to its powder, and make the silica powder and organic polymer materials realize a strong covalent bond interface through functional groups. .
The application effect of silane coupling agent is related to the selected type, dosage, hydrolysis condition, substrate characteristics, application occasions, methods and conditions of organic polymer materials.
Sphericalization of silica powder
At present, 97% of integrated circuit (IC) packaging materials use epoxy molding compound (EMC), and in the composition of EMC, silicon micropowder is the most used, accounting for 70% to 90% of the mass of epoxy molding compound. Compared with the angular silicon micropowder, the annular silicon micropowder has a higher filling rate, a smaller thermal expansion coefficient, lower thermal conductivity, less stress concentration, higher strength, and better performance of the microelectronic devices produced. Therefore, In addition to high-purity and ultra-fine particles, particle spheroidization has also become one of the development trends of silicon micropowders.
The current methods for preparing spherical silicon powder can be divided into physical methods and chemical methods. The physical methods are: flame balling method, high temperature melting spray method, self-propagating low temperature combustion method, plasma method and high temperature calcining spheroidization. Chemical methods include: gas phase method, hydrothermal synthesis method, sol-gel method, precipitation method, microemulsion method, etc. In chemical methods, due to the serious agglomeration of particles, the larger specific surface area of the product, and the large oil absorption value, it is difficult to mix with epoxy resin when a large amount is filled. Therefore, the current industry mainly adopts physical methods.
Overview of the development of silicon powder industry
The silicon powder industry is a capital, technology, and resource-intensive industry. With the development of high-tech industries, silicon micro-powders have become more widely used and used more and more. The world's demand for high-purity ultra-pure silicon powder will develop rapidly with the development of the IC industry. It is estimated that the world's demand for it will increase at a rate of 20% in the next 10 years. Ultra-fine, high-purity silicon powder has become a hot spot for the development of the industry, spherical silicon powder has become the development direction of the industry, and surface modification technology has been intensified.
Article source: China Powder Network
Important features of jet mill
The jet mill is the compressed air accelerated by the Laval nozzle into a supersonic airflow and then injected into the crushing zone to make the material fluidized (the airflow expands into a fluidized bed suspension and boiling and collides with each other), so each particle has the same state of motion .
As an important equipment for ultra-fine grinding, the jet mill has been widely used in chemical, pharmaceutical, battery materials, metallurgy, talc, quartz, graphite, abrasives, flame retardant materials, ceramics, pigments, food additives, pigments and other dry powder materials. Ultra-pure ultra-fine crushing.
Features of jet mill
In addition to fine particle size, jet mill products also have the characteristics of narrow particle size distribution, smooth particle surface, regular particle shape, high purity, high activity, and good dispersibility.
Since the compressed gas is adiabatic during the crushing process, the expansion produces a Joule-Thomson cooling effect, so it is also suitable for ultrafine crushing of low-melting, heat-sensitive materials.
Working principle of jet mill
The dry and oil-free compressed air or superheated steam is sprayed at high speed through the nozzle, and the high-speed jet moves the animal material at a high speed, causing the material to collide, rub and crush. The pulverized materials arrive at the classification area with the airflow, and the materials that meet the fineness requirements are collected by the collector. The materials that do not meet the requirements are returned to the crushing chamber to continue crushing until they reach the required fineness and are collected.
Due to the high velocity gradient near the nozzle, most of the pulverization occurs near the nozzle. In the crushing chamber, the frequency of particle-to-particle collisions is much higher than that of particle-to-wall collisions. Therefore, the main crushing effect in jet mills is the impact or friction between particles.