How to improve the grinding efficiency of jet mill
In recent years, with the development of modern industry, ultra-fine and ultra-fine pulverization technology has received more and more attention, especially the quality of the pulverization effect of raw materials in the pharmaceutical and chemical industries directly affects the subsequent process. The jet mill is the best in the current ultrafine and ultrafine grinding equipment, especially the disc type (spiral) jet mill because of its simple structure, easy disassembly and assembly, and good grinding effect. It has won many pharmaceutical and chemical companies. Favored, it has become a typical equipment for grinding high-purity, low-fineness products.
Airflow grinder requires a complete process system. How to maximize its function and reduce loss is also a crucial issue.
The compressed air after filtering and drying of the airflow grinder brings the animal material to rub against each other, so as to achieve the grinding effect; in the process of the disc airflow grinder, 80% of the electric power consumption is in the air source part of the compressed air. Making full use of compressed air is actually saving electricity to the greatest extent. How to scientifically adjust the jet mill to run under ideal conditions to improve the efficiency of the jet mill is the concern of many user manufacturers.
- Adjustment of feeding speed
The feeding speed determines the time for the materials to collide and grind in the grinding chamber. The feed speed is slow, the material stays in the grinding cavity for a long time, the number of particle cycles is large, and the grinding degree is more sufficient, so the grinding fineness is smaller; but too slow, the number of particles in the grinding cavity is too small, resulting in fewer collisions , Thus failing to achieve the desired effect. If the feed is too fast, there will be too much material in the grinding chamber, and the grinding fineness will be more effective.
Experiments have proved that uniform and stable feeding can ensure the stability of the swirling flow field in the grinding cavity. Adjust the feeding speed to make the gas-solid ratio in the grinding cavity reach the ideal state, so that the material particles can get the maximum and effective collision times, thereby increasing the grinding machine s efficiency.
- Change the speed of the grading ring or the grading wheel
The grading ring of the disc jet mill is equipped with grading. It is not as convenient and simple to adjust as the fluidized bed (classified) jet mill. Different materials have different properties, and the same working conditions have different smashing effects. It does not reach agreement, and requires a lot of experimental experience to get it.
Due to the rotation of the grading wheel, the internal swirling flow field in the crushing chamber is stabilized, so that the material is fully crushed, and the coarser materials can never pass through the grading wheel and can only return to the crushing chamber to continue crushing. Under the action of high-speed airflow, a large pulverization efficiency is achieved, and the fluidized bed jet mill also has certain advantages.
- Reasonable design of grinding nozzle
The shape of the nozzle is the key to reducing the energy loss at the nozzle. The compressed air passing through nozzles of different shapes will produce airflows of different speeds. Improper nozzle design and processing will directly lead to the failure of the speed of the pulverizing airflow or the more serious nozzle wear. The worn nozzle will deflect the airflow, causing part of the airflow to do work ineffectively and affect the pulverization efficiency.
- Other factors
In addition, there are other factors that should not be underestimated. For example, the hardness of the material to be ground is too hard, and the grinding cavity of the grinder is more severely worn. At this time, we need to replace the ultra-hard lining, such as ceramic corundum, which greatly reduces The abrasion of small materials to the grinding chamber and improve the purity of the collected materials.
In addition, in the pharmaceutical and chemical industries, materials that are easy to stick to walls such as moisture absorption and static electricity are often exposed. The materials adhere to the grinding cavity, discharge port, and receiver, which affects the progress of the entire process. Then you need to replace the special anti-sticking lining in the crushing chamber, spraying or lining the anti-sticking coating and lining in the receiver; reduce the length of the pipeline and the contact area of materials as much as possible, and improve the collection rate of materials. Effective antistatic equipment is also needed to treat materials containing static electricity.
After careful adjustment and maintenance, tap the potential of the jet mill, and use the machine more efficiently under the condition of ensuring the particle size index, which is of great significance for saving energy and reducing costs.
Application and development direction of wollastonite
Wollastonite is a calcium silicate mineral, belonging to a chain metasilicate, which is fibrous, radial, needle-like, and plate-like. Mohs hardness is 4.5~5.5, density is 2.75~3.10g/cm³, melting point is 1540℃.
Wollastonite is divided into two crystal forms: α and β. α crystals are usually granular and powdery; β crystals are usually fibrous and needle-like. The aspect ratio is usually 20:1, and the highest can reach 30:1. β crystal fibrous wollastonite has high whiteness, high resistance, high aspect ratio, low oil absorption, low dielectric constant, heat resistance, corrosion resistance, acid and alkali resistance, non-toxic, non-magnetic, and low thermal expansion coefficient. It has the characteristics of small loss on ignition and excellent mechanical properties, and has a certain affinity with plant fibers. In addition, ultrafine wollastonite powder is called "mineral fiber".
The main component of wollastonite is calcium silicate, the chemical formula is CaSiO3, the density is 2.9g/cm³, the Mohs hardness is 4.5, and the refractive index is 1.63.
The characteristics of wollastonite: non-toxic, good thermal stability, glass and pearl luster, excellent mechanical and electrical properties, chemical corrosion resistance, good dimensional stability, low absorption rate and oil absorption value, and a certain reinforcing effect.
Classification of wollastonite (by purpose)
Plastic rubber grade wollastonite: It has unique needle-like fibers, good insulation, abrasion resistance, and high refractive index. It is a good filling material for plastic and rubber products.
Coating machine wollastonite powder: the coating can get better mechanical strength, increase durability, enhance adhesion and corrosion resistance, as well as good coverage and adhesion.
Paper-making grade wollastonite powder: The use of wollastonite to make paper can improve economic benefits. Each ton of ultra-fine wollastonite powder used in papermaking can save 3.6 cubic meters of wood; compared with traditional wood pulp, each ton of ultra-fine wollastonite powder used can reduce costs by 100 to 300 yuan.
Building material grade wollastonite: non-toxic, tasteless, non-radioactive and other advantages have gradually replaced asbestos, which is harmful to human health, and become a new raw material for environmentally friendly building materials in the new century.
Ceramic-grade wollastonite powder: can greatly reduce the firing temperature, shorten the firing time, realize low-temperature fast firing at one time, save a lot of dyes, and significantly reduce product costs; at the same time, improve the mechanical properties of the product.
Friction grade wollastonite powder: needle-like structure, which greatly enhances the friction and heat resistance of the finished product. When the product is filled inside, it can improve the characteristics of friction flexibility and stability.
Product classification of wollastonite
There are mainly two types of high aspect ratio wollastonite and finely ground wollastonite.
The former is a high-end product, which is mainly used in plastics, rubber, asbestos substitutes, paints, coatings and other industries based on its physical and mechanical properties. The latter is a low-end product, mainly in the English ceramics and metallurgical industries. The SiO2 and CaO components in wollastonite provide a low expansion rate and good thermal shock resistance.
Application of wollastonite
- Plastic industry
After wollastonite is processed by special equipment, it maintains a better short fiber structure and a larger length-to-diameter ratio (15:1~20:1). It is used in polyamide (PA) 6, PA66, and polypropylene. In (PP), the physical properties, mechanical properties and heat resistance stability of plastic products have been significantly improved, and they have been promoted and applied in plastic extrusion products, hollow products, blow molding products, injection molding products and various parts.
- Rubber industry
In order to improve the friction and wear properties of rubber materials, self-lubricating materials, inorganic materials and fibrous fillers are usually added to the rubber matrix. As lubricating components, there are PTFE powder, graphite and MoS2. Inorganic materials include bentonite, wollastonite, chopped basalt fiber and nano cellulose. These modified components improve the wear resistance of rubber materials to a certain extent.
- Coating industry
Wollastonite with needle-like structure (length-to-diameter ratio 10:1~20:1), acts as a flattening agent in the coating, improves the mechanical strength of the coating film, and sometimes replaces harmful asbestos in reinforced coatings. In coatings, it is generally used for finer-grained (such as 325 mesh) and fine-grained (10μm) wollastonite powder, because it is beneficial to the hiding power of the coating. Surface-treated wollastonite can be used in industrial alkyd, epoxy and other anti-corrosion coatings to improve the corrosion resistance of metal primers and partially replace active anti-rust pigments.
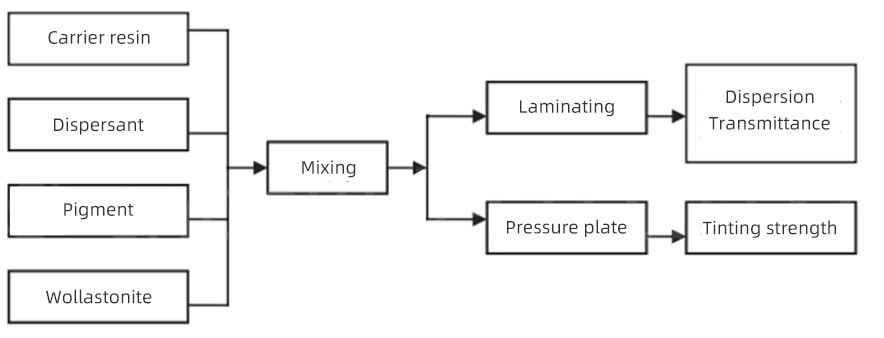
Substitution of ultra-fine needle-like wollastonite in polyethylene blue masterbatch
- Paper industry
Wollastonite powder can still maintain its unique needle-like structure after a special processing technology, so that whiteboard paper added with wollastonite powder can improve its whiteness, opacity (covering degree of the surface layer), flatness, smoothness, and adaptability. .
- Building Materials Industry
The particle size of wollastonite fiber used in the building materials industry ranges from 100 mesh to 800 mesh. The particle size, aspect ratio and purity of the fiber determine its application in different types of building materials products.
- Metallurgical Industry
About 12-15% of wollastonite in the world is used in the metallurgical industry. This is because wollastonite has low-temperature fluxing properties, stable chemical composition, high purity, and neutral alkalinity. Protective pouring provides ideal raw materials.
- Ceramic industry
Wollastonite can be used to prepare various electric porcelain, building porcelain, daily-use ceramics and brake pads.
- New material industry
The development of new materials in strategic emerging industries provides more opportunities for the application of non-metallic minerals. Wollastonite plays a role as a functional filler, and together with other non-metallic minerals, it contributes to the development and growth of the new material industry.
Development direction of wollastonite industry
- Processing technology of wollastonite needle-like powder with high aspect ratio (>15:1)
- A complete set of special processing equipment and corresponding separation equipment
- Wollastonite powder with finer particle size
- Excellent modification method and good modifier of wollastonite powder
Article source: China Powder Network
Technical characteristics of ultra-fine grinder and tips for daily maintenance
Ultra-fine grinders are now widely used in various industries. Next, we will learn about the technical characteristics of superfine grinders and the daily maintenance tips for superfine grinders.
[What are the characteristics of the current applied technology of the ultrafine grinder]
1. It is small and beautiful, light in weight, and can be moved arbitrarily; it has the characteristics of simple operation, no vibration, low noise, power saving and safety, etc., especially suitable for research institutes, laboratory sample analysis, etc.
2. Ultra-high-speed motor design, vibrating ultra-fine grinding machine for medicinal materials with high crushing fineness (most medicinal materials are crushed with a fineness of 50-300 mesh); wide grinding range: Panax notoginseng, Sanqi, frankincense, myrrh, donkey-hide gelatin, dodder, Hippocampus, astragalus, etc. can grind well.
3. The speed is fast, and the grinding time of the vibrating ultrafine grinding machine is generally no more than 3 minutes.
4. It is clean and hygienic, and does not raise dust when working. The grinding groove and blade of the vibrating ultra-fine grinder are made of stainless steel, which meets the iron-free requirements of many Chinese medicines.
5. There is basically no loss of materials, and the machine is easy to clean; grinding different medicines will never cross the color and smell.
6. The operation is simple, and the personnel do not need special training.
7. The structure is durable and economical. The blade is made of special steel, which is of the same quality as the razor, and there is no need to change the knife to crush 100-200kg pieces.
[Tips for daily maintenance of superfine grinder]
1. When the bearing oil temperature rises, you must stop immediately to check the cause of the fault and eliminate it.
2. Pay attention to the degree of wear of the parts that are easy to wear, pay attention to and prepare to replace the worn parts at any time.
3. For the surface of the bottom frame where the movable device is placed, it is necessary to remove dust and other debris to avoid the phenomenon that the movable bearing cannot move on the bottom frame when the machine encounters materials that cannot be crushed, which may lead to accidents.
4. The bearing that bears all the load of the machine is the bearing, so good lubrication has a great relationship with the service life of the bearing. It can directly affect the service life and operation rate of the machine. Therefore, the cleanliness of the injected lubricating oil must meet the standard and the seal is good.
5. The installed wheel tyres are prone to looseness and must be checked frequently.
6. Pay attention to whether the working conditions of each part of the machine are normal.
7. If the rotating gear is running, if there is an impact sound, it must be stopped in time for inspection and the malfunction should be eliminated.
The functional characteristics and common problems of air classifier
The air flow classifier is a professional gas classification equipment, which is widely used in the field of product processing. So what are the performance characteristics of the air classifier? What problems often occur with air classifiers?
[What are the performance characteristics of the air classifier]
Airflow classifier is a commonly used equipment in the field of product processing. Only with a classifier can more precise raw materials be processed. Only with these extremely high-precision raw materials can companies produce better quality products.
Air classifiers commonly used in enterprises generally have the following performance characteristics:
1. It is suitable for the fine classification of dry-process micron products. It can classify spherical, flake, and needle-shaped particles, and can also classify particles of different densities.
2. The particle size of the graded products can reach D97: 8~150 microns, the product size is steplessly adjustable, and the variety is extremely convenient to change.
3. The classification efficiency (extraction rate) is 60%~90%, and the classification efficiency of materials with good fluidity is high, otherwise the efficiency is reduced.
4. Vertical or horizontal grading turbine device is adopted, with low speed, wear resistance and low system power configuration.
5. Multiple air classifiers can be used in series to produce products with multiple particle sizes at the same time.
6. It can be used in series with ball mill, vibration mill, Raymond mill and other grinding equipment to form a closed loop.
7. Large output, low energy consumption and high classification efficiency.
8. The particle size is concentrated. The machine uses an original impeller for classification. The stable classification technology and special sealing measures effectively prevent the leakage of coarse particles, so that the product has no large particles, and the particle size is concentrated and the classification accuracy is high.
[What are the common problems of air classifiers]
The processing accuracy and classification accuracy of product raw materials has always been the focus of the processing industry, because in some industries product raw materials will greatly affect the related quality of a product. Air flow classifier is a kind of air flow classification equipment. The classifier, cyclone separator, dust collector, induced draft fan, etc. form a complete set of air flow classification equipment.
1. What does the wind power of the induced draft fan of the air classifier have to do with?
The wind power of the induced draft fan of the classifier is related to the actual production goal of the enterprise. The wind power is selected by examining the particle size of the related products.
2. How to debug the air grading equipment?
The adjustment of the grading machine generally depends on its equipment structure, and the spacing of the grading slices, etc., and it must be adjusted to a suitable production environment in accordance with the actual production situation.
3. What are the main applications of the air classifier?
The classifier is mainly used in the fine classification of micron-level products. The classified products can be better classified, providing reliable guarantee for the production of products by enterprises.
Several Methods to Improve the Grinding Efficiency of Ball Mill
The low grinding efficiency of the ball mill, low processing capacity, high production energy consumption, and unstable product fineness are the problems that most concentrators will encounter. How to effectively improve the grinding efficiency of the ball mill is an important issue.
- Change the grindability of raw ore
The hardness, toughness, dissociation and structural defects of the original ore determine the difficulty of grinding. If the hardness is small, the ore is easy to grind, the wear of the mill liner and the steel ball is small, and the energy consumption is small; otherwise, the situation is just the opposite. The nature of the original ore directly affects the productivity of the factory.
In production, if it is difficult to grind ores or needs to be finely ground, if economic and on-site conditions permit, a new treatment process can be used to change the grindability of the ore:
One method is to add some chemicals in the grinding process to improve the grinding effect and improve the grinding efficiency.
Another method is to change the grindability of the ore, such as heating the minerals in the ore, changing the mechanical properties of the entire ore, and reducing the hardness.
- More crushing and less grinding to reduce the grinding particle size
If the grinding particle size is large, the mill needs to perform more work on the ore. In order to achieve the required grinding fineness, the workload of the ball mill is bound to increase, so energy consumption and power consumption will also increase.
In order to reduce the size of the grinding feed, it is required that the particle size of the pulverized product should be small, that is, "more pulverize and less grind". Moreover, the grinding efficiency is significantly higher than the grinding efficiency, and the grinding energy consumption is relatively low, about 12%-25% of the grinding energy consumption.
- Reasonable filling rate
When the speed of the ball mill is fixed and the filling rate is large, the steel ball will hit the material many times, the grinding area is large, the grinding effect is strong, but the power consumption is also large. The filling rate is high, which is easy to change the motion state of the steel ball and reduce the impact effect on the large particle material. On the contrary, the filling rate is too small, and the grinding effect is poor.
At present, many mines set the filling rate to 45%~50%, which is not necessarily strictly reasonable, because the actual conditions of each beneficiation plant are different. Copying the ball load data of others cannot achieve the ideal grinding effect. It should be determined according to the situation. .
- Reasonable ball size and proportion
Due to the point contact between the steel ball and the ore in the ball mill, if the diameter of the ball is too large, the crushing force is also great, causing the ore to break along the direction of the penetration force instead of along the interface. Crushing is not selective and cannot meet the purpose of grinding.
In addition, in the case of the same steel ball filling rate, the steel ball diameter is too large, resulting in too few steel balls, the possibility of crushing is low, the phenomenon of excessive crushing is aggravated, and the product particle size is uneven. Because the ball is too small, the crushing force on the ore is small, and the grinding efficiency is low. Therefore, the correct ball size and ratio have an important influence on the grinding efficiency.
Application of Ultra-fine Grinding Technology in Food Processing
Ultra-fine grinding technology is a new technology developed in the past 20 years. The so-called ultra-fine grinding refers to the use of mechanical or hydrodynamic methods to overcome the internal cohesive force of solids to grind them, thereby grinding the material particles of more than 3 mm to 10-25 microns. A material processing high-tech produced by the development of high-tech. Ultra-fine powder is the final product of ultra-fine grinding. It has special physical and chemical properties that ordinary particles do not have, such as good solubility, dispersibility, adsorption, and chemical reaction activity. Therefore, ultra-fine powders have been widely used in many fields such as food, chemicals, medicine, cosmetics, pesticides, dyes, coatings, electronics and aerospace.
- Technical Features
Fast speed and low temperature grinding: The ultra-fine grinding technology uses supersonic jet grinding, cold slurry grinding and other methods, which is completely different from the previous pure mechanical grinding methods. There will be no local overheating during the grinding process, and it can even be ground at a low temperature. The speed is fast and can be completed in an instant, so the biologically active ingredients of the powder are retained to the greatest extent, so as to facilitate the production of the required high-quality products .
Fine particle size and uniform distribution: Due to the use of supersonic airflow grinding, the distribution of forces acting on the raw materials is quite uniform. The setting of the classification system not only strictly restricts large particles, but also avoids over-grinding, and obtains ultra-fine powder with uniform particle size distribution. At the same time, the specific surface area of the powder is greatly increased, so that the adsorption and solubility are correspondingly increased. .
Save raw materials and improve utilization: After the object is ultra-finely ground, the ultra-fine powder with a near nanometer particle size can generally be directly used in the production of preparations, while the products of conventional grinding still need some intermediate links to meet the requirements of direct use and production , This is likely to cause waste of raw materials. Therefore, this technology is especially suitable for grinding precious and rare raw materials.
Reduce pollution: Ultra-fine grinding is carried out in a closed system, which not only avoids the pollution of the surrounding environment by micro-powder, but also prevents dust in the air from polluting the product. Therefore, by using this technology in food and medical health products, the microbial content and dust can be effectively controlled.
- Grinding method
Grinding medium grinding: Grinding medium grinding is the process of grinding material particles by means of the impact generated by the moving grinding medium (grinding medium) and the non-impact bending, squeezing and shearing forces. The grinding media pulverization process is mainly grinding and friction, namely extrusion and shearing. Its effect depends on the size, shape, ratio, movement mode, filling rate of the material, and the mechanical characteristics of the grinding of the material. There are three types of typical media grinding equipment: ball mill, stirring mill and vibration mill.
The ball mill is a traditional equipment used for ultra-fine grinding, and the product size can reach 20-40 microns. When the particle size of the product is required to be below 20 microns, the efficiency is low, the energy consumption is large, and the processing time is long. Stirring mill is developed on the basis of ball mill, mainly composed of grinding container, agitator, disperser, separator and feed pump. When working, under the action of centrifugal force generated by the high-speed rotation of the disperser, the grinding medium and the particle slurry produce impact shearing, friction and squeezing to grind the particles. The stirring mill can achieve ultra-micronization and homogenization of product particles, and the average particle size of the finished product can reach a few microns at least. Vibration mill is to grind particles by using the effects of impact shear, friction and extrusion produced by high-frequency vibration of the grinding medium. The average particle size of the finished product can reach 2-3 microns or less, and the pulverization efficiency is much higher than that of the ball mill. The processing capacity is more than 10 times that of a ball mill with the same capacity.
Airflow ultra-fine grinding: The jet mill can be used for ultrafine grinding. It uses compressed air or superheated steam, and the supersonic high turbulent airflow generated by the nozzle as the carrier of the particles, and the impact backlog occurs between the particles or between the particles and the fixed plate , Friction and shearing, etc., so as to achieve the purpose of grinding. There are six major types of airflow stainless steel grinders: disc type, circulating tube type, target type, collision type, rotary impact type, and fluidized bed type. Compared with ordinary mechanical ultra-fine stainless steel pulverizer, the airflow stainless steel pulverizer can grind the product very fine (the fineness of the powder can reach 2-40 microns), and the particle size distribution range is narrower, that is, the particle size is more uniform. Because the gas expands at the nozzle to reduce the temperature, there is no accompanying heat during the grinding process, so the grinding temperature rise is very low. This feature is particularly important for ultra-fine grinding of low-melting and heat-sensitive materials. However, the energy consumption of air jet grinding is large, and the energy utilization rate is only about 2%, which is several times higher than other grinding methods.
It is worth pointing out that it is generally believed that the particle size of the product is directly proportional to the feeding speed, that is, the larger the feeding speed, the larger the product particle size. This understanding is not comprehensive. This statement is reasonable when the feeding speed or the particle concentration in the stainless steel pulverizer reaches a certain value. Because the feeding speed increases, the particle concentration in the stainless steel pulverizer also increases, and particle crowding occurs. Even the particles flow like a plunger. Only the particles at the front of the "plunger" have the possibility of effective collision. The particles only collide and rub each other at a low speed, and generate heat. However, this does not mean that the smaller the particle concentration, the smaller the product size, or the higher the grinding efficiency. On the contrary, when the particle concentration is low to a certain level, there will be no chance of collision between the particles and the grinding efficiency will be reduced.
What are the factors that affect the grinding efficiency of jet mills?
Jet mill is a kind of equipment that uses high-speed air flow energy (300~500m/s) or superheated steam (300~400℃) to make powders collide, collide, and rub against each other to make them grind. The nozzle sprays high-pressure air or high-pressure hot air, and then rapidly expands to form a high-speed airflow. Due to the large velocity gradient near the nozzle, most of the grinding occurs near the nozzle. The collision frequency between particles in the grinding chamber is much higher than the collision frequency between particles and the wall, that is, the main function of the jet mill is the collision between particles.
The control of the final particle size of the product by the jet mill mainly depends on the raw material particle size, crushing pressure, feeding pressure, feeding speed and other parameters. The logical relationship between the pneumatic grinding device and these parameters is specifically: the smaller the particle size of the raw material, the higher the grinding efficiency, on the contrary, the larger the particle size, the lower the grinding effect. When the grinding pressure and feed pressure are constant, reducing the feed rate will make the product finer, and increasing the feed rate will make the product coarser. When the feed rate is constant, increase the grinding pressure, the product size will become finer, and reduce the grinding pressure, the product will become coarser.
Therefore, particle size control is achieved by adjusting the parameters in the grinding process of the jet mill to achieve different pulverization finenesses. Before pulverization, the relationship between the feeding speed and pressure must be determined first, and then the appropriate pulverization parameters must be determined to meet different requirements. Granularity requirements.
The advantage of the jet mill is that it grinds no pollutants. After grinding, the compressed supersonic airflow speed decreases and the volume increases. It is an endothermic process and has a cooling effect on the material. It is especially suitable for ultrafine grinding. The jet mill uses supersonic airflow to accelerate the speed of particles, collide with each other or grind materials to achieve the grinding effect.
In order to increase the collision speed, a number of evenly distributed sub-nozzles are set around the main nozzle to accelerate the material particles around the main nozzle into the central area of the main stream. The feed nozzle is located in the center of the main nozzle, and the fluidized particles can be directly sucked into the center of the main nozzle to achieve a higher collision velocity.
At present, the jet milling equipment used in industry includes: flat plate, circulating tube, target type, convection type, fluidized bed type.
Influencing factors of the grinding effect of jet mill
Research results show that the grinding effect of the jet mill is affected by factors such as gas-solid ratio, feed particle size, working fluid temperature, and working fluid pressure.
- Gas-solid ratio
If the gas-solid ratio is too small, the gas flow energy will be insufficient, which will affect the fineness of the product; on the contrary, if the gas-solid ratio is too large, it will not only waste energy, but also deteriorate the dispersion performance of certain materials.
- Feed size
When grinding hard materials, the particle size requirements of the feed materials are also stricter. For titanium powder, the crushed calcined material should be controlled at 100~200 mesh; the surface treatment material grinding is generally 40~70 mesh, not more than 2~5 mesh.
- Working fluid temperature
At high temperatures, the gas flow rate in the working fluid increases. Take air as an example. The critical velocity at room temperature is 320m/s. When the temperature rises to 480℃, the critical velocity can be increased to 500m/s, and the kinetic energy is also increased by 150%. The effect is favorable.
- Pressure of work material
The working hydraulic pressure is the main parameter that produces the jet flow rate and affects the grinding fineness. Generally speaking, the higher the working pressure and the faster the working speed, the greater the kinetic energy, which mainly depends on the grindability and fineness requirements of the material.
- Grinding aids
During the grinding process of the jet mill, if a suitable grinding aid is added, not only the grinding efficiency can be improved, but also the dispersibility of the product in the medium can be improved.
The principle of daily maintenance of ball mill
Ball mills can play a greater role in industrial production only after good daily maintenance.
1. All lubricating oil should be discharged when the mill is put into continuous operation for one month, thoroughly cleaned, and replaced with new oil. In the future, the oil change will be carried out approximately every 6 months in conjunction with the middle repair.
2. The lubrication condition and oil level of each lubrication point are checked at least every 4 hours.
3. When the mill is running, the temperature of the main bearing lubricating oil should be lower than 55°C.
4. When the mill is running normally, the temperature rise of the transmission bearing and reducer should not exceed 60℃, and the high temperature should be lower than 70℃.
5. The large and small gears drive smoothly without abnormal noise.
6. The ball mill runs smoothly without strong vibration.
7. Check the motor current from time to time for no abnormal fluctuations.
8. During routine maintenance, ensure that the connecting fasteners are not loose, and there is no oil leakage or water leakage on the joint surface.
9. The wear condition of the steel ball should be added in time.
10. If an abnormal situation is found, the grinding should be stopped immediately for maintenance.
11. The mill liner should be replaced when it is 70% worn or there are 70mm long cracks.
12. When the liner bolts are damaged and the liner becomes loose, replace it.
13. Check that the main bearing should be replaced when it is severely worn.
These maintenance principles seem cumbersome, but in fact the operation is very simple. As long as the production of the ball mill is treated seriously and carefully, and the daily maintenance is done, the economic benefits that the ball mill can bring will be huge.
How to solve the sudden failure of the ball mill
Ball mill equipment is the equipment that accounts for a considerable investment in the entire concentrator, accounting for more than 50%. Therefore, ensuring the normal operation of the ball mill is a necessary condition to ensure the normal production of the entire concentrator. However, when the ball mill is in use, some sudden failures often occur, which affects production efficiency. So how to effectively solve or avoid these sudden failures?
Sudden failures of ball mills are generally caused by multiple reasons such as long-term high-speed operation and improper operation.
- The stator coil of the ball mill is broken down
In the entire system of the ball mill, there will be iron-containing dust in the air around the material. After a long time of operation, the iron-containing dust will adhere to the coil of the ball mill stator. When it reaches a certain thickness, it will cause the surface of the stator coil. A short-circuit discharge situation has occurred. When the short-circuit phenomenon occurs many times, the insulator of the coil will be damaged, causing the phenomenon of sparking and breakdown, causing the ball mill to stop running. Without a backup motor, the grinding work is difficult to continue. At this point, the breakdown coil should be cut off immediately, scientific protection measures should be adopted, and the ball mill can be restarted to continue production.
- The sliding shaft of the ball mill is scratched
After the sliding shaft of the ball mill has been worn for a long time and reaches a certain thickness, it is difficult to combine the spherical body of the ball mill with the tile lining, and scratches will occur. Generally, this kind of situation occurs because the clinker temperature of the hollow shaft is too high, and the temperature of the outer surface of the hollow shaft is also high, which causes the lubricating oil to be too diluted, loses viscosity, and is difficult to form a good oil film, resulting in bushings and journals. Friction generates heat and heats up rapidly, causing the surface of the tile lining to be melted and scratched.
If there is no spare spherical tile-hour, you can only stop the machine for inspection and repair the tile surface before continuing to use it. The smoothness of the scratched surface can be restored by frustrating, cutting, grinding, etc., while the undamaged part needs to be scraped out of a micro oil groove to repair the tile. And unload the materials and grinding media in the ball mill, and use manual methods to rotate the barrel for no-load grinding. When it reaches a certain level, it will run in conjunction with the transmission part for a no-load test, and then load the materials and grinding media into the ball mill for load operation, so that the ball mill can return to normal operation.
- The barrel screw and hollow shaft of the ball mill are broken
In the process of connecting the cylinder body and the hollow shaft of the ball mill, the cylinder body needs to be drilled through holes with the flange, and the pins are connected through the turnbuckles. The through holes only need ordinary screws to connect. The reamed holes are mainly used for limiting and Positioning role.
After long-term operation of the ball mill, due to thermal expansion and contraction, distortion, high temperature corrosion, water vapor corrosion, etc., the matching size of the pin hole and the reamed hole will change, and the phenomenon of looseness will occur, which makes it difficult to achieve position limitation. Because of the twisting, the screw starts to loosen, causing the cylinder and the hollow shaft to periodically displace. If the screw is stretched for a long time, the screw will break.
According to many years of experience, after this kind of failure occurs, the screw can be changed to a hinge pin for connection. At present, there has been no phenomenon of hinge pin fracture.
- The temperature rise of the sliding bearing of the ball mill
During the operation of the ball mill, the base part of its head slides and the temperature of the bearing suddenly rises. This phenomenon is mostly caused by the sinking of the base part of the head, the overall movement of the grinding body and the tilting. The spherical bush shoulder of the ball mill and the flange root of the hollow shaft undergo squeezing contact and rotating friction, which generates heat and causes the temperature to rise rapidly. high. This situation may cause the ball mill to tilt. The meshing of the large ring gear and the pinion gear will form an axial angle, which will cut the teeth each other, which will increase the difficulty of meshing, cause loud noise and increase the vibration, and will cause the ball mill to stop in severe cases.
After this phenomenon occurs, it is necessary to stop the machine for inspection, weld and lengthen the grounding bolts, wedge the shim iron, raise the bearing seat, and control the temperature of the sliding bearing and the sound of the transmission part.
Wide range of product applications for air classifiers
Features of Air Classifier:
1. Large output, low energy consumption and high grading efficiency.
2. Concentration of particle size: The machine uses an original vertical impeller for classification. The stable classification technology and special sealing measures effectively prevent the leakage of coarse particles, so that the product has no large particles, centralized particle size and high classification accuracy.
3. Reasonable structure: products with 1-6 particle sizes can be produced at the same time according to user requirements.
4. Strong applicability: It can be combined with various mills (jet mill, mechanical mill, ball mill, Raymond mill, vibration mill, etc.) to form a closed-circuit or open-circuit combined operation.
5. High degree of automation.
Working principle of air classifier:
Qualified fine powder is carried by the updraft into the turbo classifier above the fluidized bed. The classifier classifies qualified materials and enters the cyclone collector (if products with several particle sizes are required, multiple vertical turbines are added Classifier). The finer tail material is carried by the airflow into the bag filter. After being filtered by the bag, the tail material enters the discharge port at the lower part of the dust collector, and the pure air is emptied.
The main components of the machine: the standard configuration is a vertical turbine classifier. The crushing and classification are coordinated and completed synchronously. The speed of the classifier can be adjusted by frequency conversion, and the product fineness can be adjusted arbitrarily. If a processing process requires products with multiple granularities, two to four can be installed on the basis of a standard classifier to make this machine a two-connected-five-connected crushing and grading machine.
Application range: The crushing mechanism of this machine determines its wide application range and high fineness of the finished product. Typical materials include: superhard diamond, silicon carbide, metal powder, etc., high purity requirements: ceramic pigments, medicine, biochemical Etc. Low temperature requirements: medicine, PVC. By changing the ordinary air in the air source to inert gases such as nitrogen and carbon dioxide, the machine can be used as an inert gas protection device, suitable for the crushing and classification of inflammable, explosive, and oxidizable materials.
Airflow classifier product application:
1. High hardness materials: silicon carbide, various corundum, boron carbide, alumina, zirconia, garnet, zircon sand, diamond, etc.
2. Non-metallic minerals: quartz, graphite, kaolin, calcium carbonate, mica, barite, mullite, medical stone, wollastonite, talc, pyrophyllite, etc.
3. Chemical industry: aluminum hydroxide, silica gel, various dyes, epoxy resin, various additives, etc.
4. Food and medicine: pollen, hawthorn, pearl powder, Ganoderma lucidum, various vegetable powder, various Chinese herbal medicines, various health products, cosmetics, antibiotics, etc.
5. Metal materials: aluminum powder, magnesium powder, zinc powder, tin powder, copper powder, etc.
6. Other materials: ceramic materials, refractory materials, electronic materials, magnetic materials, rare earth materials, phosphors, copy material powders, etc.